Surface Preparation
Optimizing Surface Preparation for Rigid Substrates in UV/LED Inkjet Printing
Achieving superior adhesion in UV/LED inkjet printing on rigid substrates requires meticulous surface preparation. The integrity of a print is only as strong as its bond to the substrate, making surface treatment a critical step in ensuring durability, vibrancy, and longevity. At Fluid Color, we emphasize the importance of proper surface preparation techniques to maximize adhesion and enhance print quality. Proper preparation minimizes ink delamination, improves scratch resistance, and ensures long-term performance in both indoor and outdoor applications.
Understanding Surface Energy and Its Role in Adhesion
Surface energy plays a key role in determining how well ink adheres to a substrate. Materials with low surface energy, such as plastics and certain composites, naturally repel ink, leading to poor adhesion and potential print failures. Proper surface preparation increases surface energy, allowing for better wetting and bonding of UV-curable inks. Surface energy is measured in dynes per centimeter, and substrates typically require a minimum surface energy of 40-42 dynes/cm for optimal ink adhesion. Testing surface energy with dyne pens before and after treatment can help verify adhesion readiness.
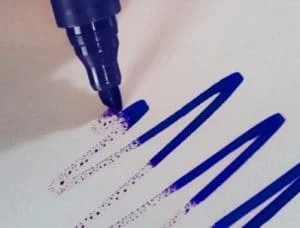
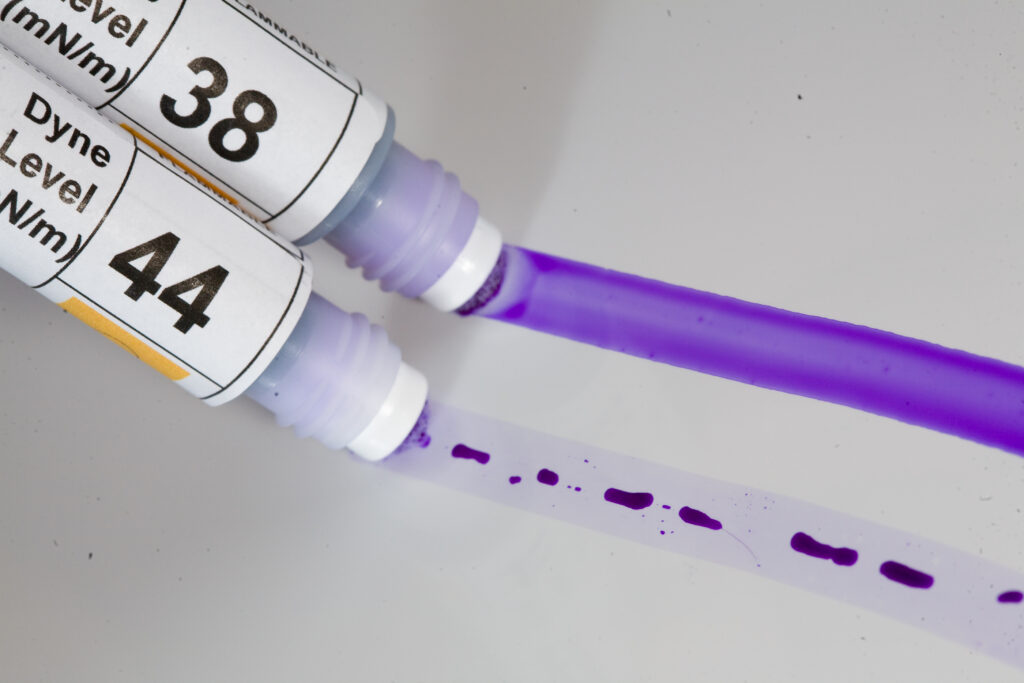
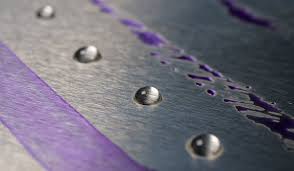
Common Surface Preparation Techniques
To ensure optimal adhesion, several surface treatment methods can be employed based on the substrate type:
1. Cleaning and Degreasing
Before any advanced treatment, substrates should be free of dust, oils, and contaminants. Using isopropyl alcohol (IPA) or specialized degreasers helps remove residues that could interfere with adhesion. A clean surface provides a solid foundation for the subsequent treatment. For industrial applications, ultrasonic cleaning or vapor degreasing may be used for highly sensitive materials.
2. Mechanical Abrasion
For materials such as metals, glass, and some plastics, light sanding or scuffing with an abrasive pad creates a micro-roughened surface. This increases the contact area for the ink and improves adhesion. Sandblasting or bead blasting can be used for more aggressive surface modification, especially for applications requiring heavy-duty adhesion performance.
3. Flame Treatment
Flame treatment involves exposing the substrate to an open flame (propane, MAPP gas, or Pyrosil) to oxidize the surface and increase surface energy.
- Propane and MAPP Gas: Used primarily for plastics such as polyethylene and polypropylene, flame treatment alters the molecular structure to enhance ink adhesion. This method is fast and cost-effective but requires precision to avoid overheating or melting the substrate.
- Pyrosil Treatment: A more advanced variation, Pyrosil deposits a silicate layer on the surface, which improves adhesion on glass and metal substrates. This treatment provides a chemically active surface for superior bonding.
4. Corona and Plasma Treatment
Both corona and plasma treatments are widely used in industrial printing applications.
- Corona Treatment: Uses high-voltage electrical discharge to improve the wettability of polymer surfaces. It is effective for short-term adhesion improvements and works well on films and plastics. However, the effects diminish over time, requiring treated materials to be printed shortly after treatment.
- Plasma Treatment: A more controlled process, plasma treatment alters the substrate’s chemical composition and can be tailored for specific materials, making it highly effective for glass, composites, and high-performance plastics. Atmospheric plasma is effective for large-format substrates, while vacuum plasma offers more intensive modification at a molecular level.
5. Primers and Adhesion Promoters
When mechanical or chemical treatments are insufficient, primers provide a bonding layer between the substrate and ink. UV adhesion promoters specifically designed for non-porous materials help bridge the gap where direct adhesion is challenging. Primers can be solvent-based, water-based, or UV-curable, depending on the substrate and application requirements. Adhesion promoters containing silane compounds are particularly effective for improving ink bonding on glass and ceramics.
Choosing the Right Preparation for Your Application
Each substrate presents unique challenges. Selecting the appropriate treatment depends on the material, production environment, and end-use requirements. At Fluid Color, we guide our customers in choosing the best preparation methods to ensure maximum adhesion and print longevity. For example:
- Acrylic & Polycarbonate: Benefit from plasma treatment or UV-curable primers for strong adhesion.
- Glass & Metal: Pyrosil or silane-based primers enhance adhesion significantly.
- Polyethylene & Polypropylene: Require flame or corona treatment due to their low surface energy.
- Powder-Coated & Painted Surfaces: Mechanical abrasion combined with a primer ensures strong ink adhesion.
By implementing proper surface preparation techniques, print providers can achieve superior results, reduced production waste, and increased customer satisfaction. As UV/LED inkjet technology continues to evolve, mastering adhesion science remains key to unlocking the full potential of digital printing on rigid substrates.
For more information on Fluid Color’s industry-leading UV/LED printing solutions, contact our team today.